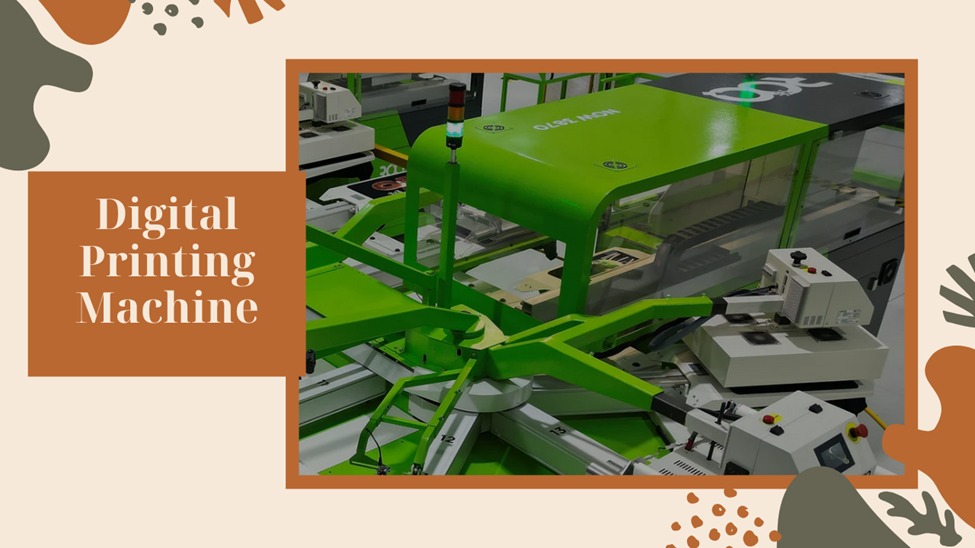
Digital printing has revolutionized the textile and paper industries by enabling high-quality, OnDemand production with minimal setup. Unlike traditional methods like offset or screen printing,
digital printing eliminates the need for plates, allowing direct transfer of digital designs onto
substrates using advanced inkjet technology. This article provides a step-by-step operational
guide for digital printing machines, emphasizing safety, quality, and efficiency.
1. Pre-Treatment and Fabric Preparation
Why Pre-Treat?
Pre-treatment ensures optimal ink absorption and color fastness, particularly for natural fibers
like cotton or silk. A chemical solution (e.g., ROQ Primer) is applied to the fabric to prepare its
surface for printing.
Procedures –
- Apply white Base: Ensure an even, uniform layer; for dark fabrics, apply a white base
via screen printing if required - Dry the Fabric: Pass the fabric through a dryer (e.g., Dryer) at 150–180°C to fix the pretreatment chemicals.
- Apply Pre-Treatment: Apply a chemical Pre-treatment solution (e.g., Primer) to evenly
across the fabric. - Dry the Fabric Post Pre-treatment: Dry the fabric according to the solution
manufacturer’s instructions. - Store Properly: Keep pre-treated fabric in a dust-free & humidity-controlled
environment until printing
2. Machine Setup and Calibration
Loading the Substrate –
- Fabric: Place the fabric is aligned straight on designated sticky pallets, with no wrinkles
or creases. - Print Heads: Perform a nozzle check and cleaning cycle if needed. Replace clogged or
damaged print heads. - Calibration: Perform automatic or manual calibration and use static eliminators to avoid
misfeeds. Adjust the height for fabric thickness (up to 20 mm) to ensure optimal
printhead distance. - Inspect the Machine: Check for any visible damage or loose components. Ensure all
cables and hoses are securely connected.
Ink System Preparation
- Ink Selection: Use CMYK, extended chambers (Red, green), or specialty inks (metallic,
white) based on design requirements. - Ink Refill: Ensure sufficient ink is available; refill if necessary.
- Prime the Print Heads: Flush ink lines to remove air bubbles and ensure consistent
droplet formation.
3. Design Preparation and Software Configuration
Artwork Guidelines –
- Design Software: Create or obtain the digital design using compatible graphic design
software (e.g., Adobe Photoshop, ROQ Studio) - File Format: Use high-resolution TIFF, PNG, or PDF files with bleed margins (3–5
mm). - Color Management: Calibrate colors and resolution as needed
RIP Software Workflow
- Import the design into Raster Image Processor (RIP) software (e.g., ROQ Studio).
- Set parameters: resolution (minimum 300 DPI), print speed (Minimal), and ink density7.
- Adjust print settings on small fabric sample (quality, speed, color mode)
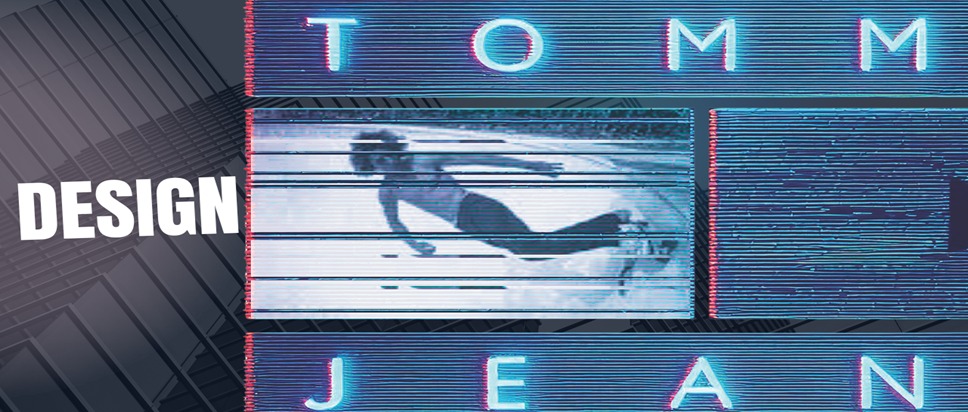
4. Printing Process Execution
Inkjet Printing Mechanism –
- Load the digital design into the machine’s software interface.
- The print heads move back and forth (e.g., Bi-directional or Uni-directional), spraying
tiny ink droplets onto the fabric precisely as per the digital design. - Multi-pass printing (4–16 passes) enhances color depth and gradient smoothness.
- Configure print parameter (resolution, color profile, print speed, number of passes) based
on the fabric and ink type
Monitoring and Adjustments –
- Real-Time Checks: Inspect for banding, misalignment, or nozzle clogs.
- Consistency: Start the print job and monitor the first few prints for consistency.
- Top Covering: Applying top covering via screen printing.
- Drying: Allow prints to dry fully before handling (if required)
- Troubleshooting:
o Banding: Clean print heads or increase passes.
o Color Shift: Recalibrate RIP software. - Unload Printed Materials: Carefully remove prints to avoid smudging or damage
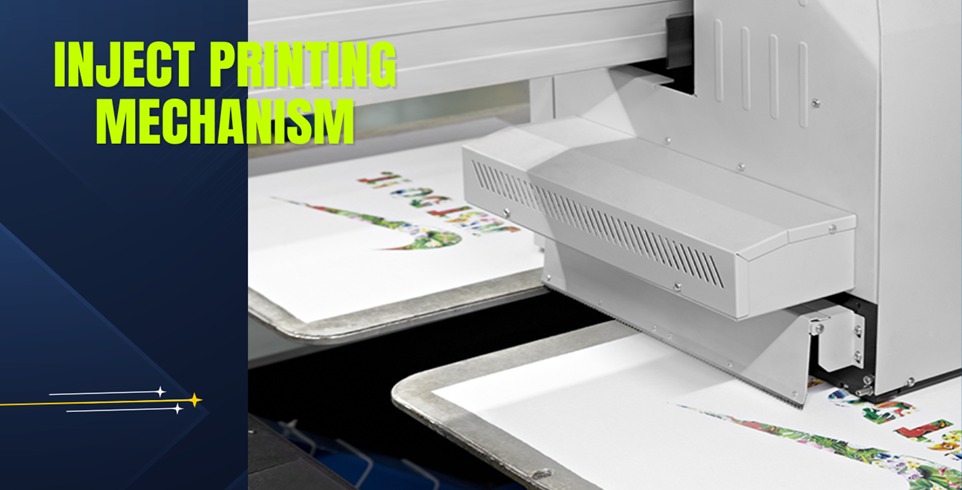
5. Post-Printing Processing
Drying and Fixation –
- Curing: After Printing, transfer the fabric through a drying or curing station (heated
chamber, infrared dryer) to set the ink. - Heat Pressing: Based on fabric and ink specification, extra fixation may be required
utilizing steam, dry heat, or pressure. - Durability: Ensure the fabric is completely dry and the colors are fixed for durability
Washing and Finishing –
- Wash the printed fabric according to the customer’s requirements.
- Dry the fabric again if necessary.
- Inspect for defects like crocking or color bleed.
6. Quality Control
Inspection Protocols –
- Print Quality: Scrutinize the printed fabric for defects (color inconsistencies, misprints,
incomplete fixation). - Color Fastness: Assess color fastness and wash resistance through standard testing
methods. - Dimensional Stability: Measure shrinkage after washing/curing (max 1cm).
- Report: Record any issues for corrective action and continuous improvement.
7. Machine Maintenance
Daily –
- Check the level of ink into the sub-tanks.
- Take the machine out of standby mode for cleaning (Stoppage/CAP will be max
72hours). - Clean print heads and ink lines frequently with cleaning solutions as per manufacturer’s
guidelines. - Remove the CAP system and rinse it with distilled water.
- Keep the machine temperature (printing area) between 20-25 °C and the humidity
between 50-70%. - Carry out a nozzle test and keep record to monitor the degradation of the print head.
- Empty the waste tanks.
Weekly –
- Switch off the machine and clean the encoder strip using isopropyl alcohol.
- Check the level of ink into the sub-tanks.
- Lubricate the carriage and wipe system linear guide blocks using lubricants
recommended by the manufacturer. - Recalibrate the vacuum sensor.
- Carry out scheduled maintenance checks to guarantee optimal functioning of the
machine.
Monthly –
- Check the channels of the peristaltic pumps and replace them in case of visible wear
(please contact the technical support). - Clean the main ink tanks or replace them, if necessary.
Yearly –
- Replace the ink filters (if necessary).
- Replace the wiper’s rubber.
- Clean the ink circuit and check for any wear on any part of it.
- Replace the degassing.
Summary of Maintenance –
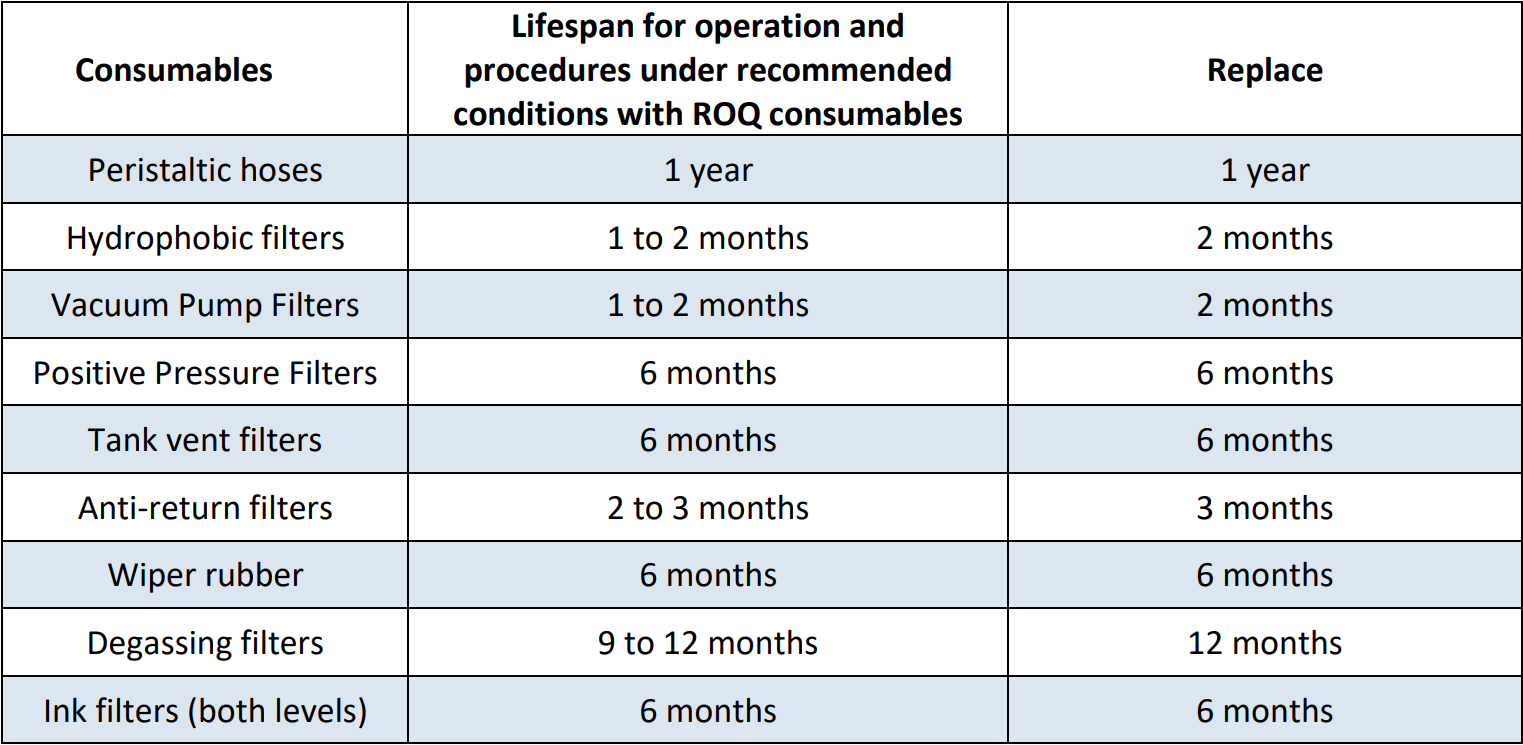
8. Safety and Best Practices
Hazards –
- Incorrect handling may cause accidents.
- Do not handle this digital printer if you are fatigued or under the influence of medication.
- Do not use the digital printer inappropriately or in excess of its working capacity,
otherwise it may result in injury or fire hazard. - Use only accessories (consumables, AC accessories) recommended by the manufacturer.
- Improper operation or handling of these components may result in personal or material
damage.
Safety –
- Ensure proper airflow to dissipate solvent fumes (e.g., ethanol, glycol).
- Prohibit smoking near machines and store inks in flame-resistant cabinets.
- Wear appropriate PPE (gloves, safety glasses, etc.).
- Handle the digital printer and screen-printing machine carefully and avoid any contact
with the equipment during its operation. - Do not expose parts of the body in accident-prone areas.
Shutdown Procedure –
- Clean the printheads and surrounding areas using a clean cloth with solution
(recommended by manufacturers). - Pour the cleaning solution into the CAP (respecting level between ½ or ¾).
- Set the machine standby or turn off the machine via control panel (max 72 hours).
- It will automatically position itself over the CAP’s.
- Cover the machine to protect it from dust.
9. Conclusion
Mastering digital printing machine operation requires attention to detail at every stage—from
substrate preparation to post-processing. By adhering to these guidelines, operators can achieve
vibrant, durable prints while maximizing machine lifespan and productivity. As digital printing
technology evolves, staying updated on advancements like AI-driven color matching and 3D
texture printing will further enhance operational excellence.
Written By –
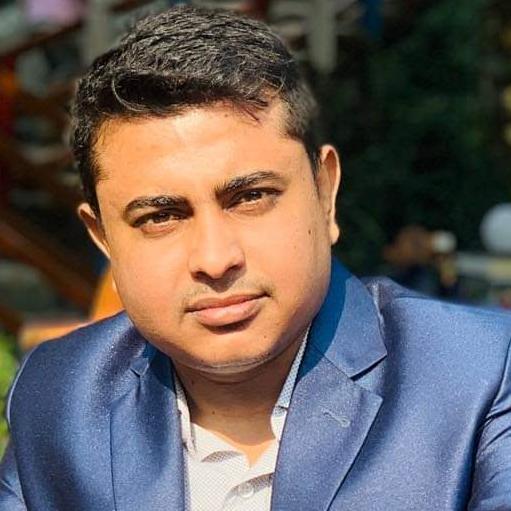
Engr. Iqubal Hossain
Joint Secretary – Organizing Panel (BDEEF)
Engr. Iqubal is a seasoned printing production specialist with a passion for precision and creativity. With years of hands-on experience in delivering high-quality print solutions, he bridges the gap between technical excellence and artistic vision. Connect with him to discover more about the art and science behind impactful printing.